
Power Quality problems come with a lot of consequences and cost. Costing organizations millions of dollars, causing systems and equipment downtime with loss of productivity. The culprits are
- Lightning
- Utility Automatic Breaker Reclosure
- Utility Capacitor Switching
- Commercial high rises without enough distribution transformers
- Gen-sets not sized for harmonic loads
- Applying P.F correction capacitors without considering the effects of harmonics
- In-rush currents from high torque motor loads started across the line
- Undersized neutrals at the panel board
- Running power and signal cables together
- Loose conduit connections and lack of green wire grounding conductors
- Shared neutrals on branch circuits
- Laser printers and copiers sharing branch circuits with sensitive loads mis-wired receptacles.
- Data cables connected to different ground references at each end.
Power quality solutions

There are four ways to mitigate and eliminate power quality problems
- Designing equipment and electrical systems to prevent electrical disturbances from causing equipment or systems to malfunction.
- Analyzing the symptoms of a power quality problem to determine its cause and solution.
- Identifying the medium that is transmitting the electrical disturbance, reducing or eliminating the effect of the medium
- Treating the symptoms of the power quality problem by the use of power conditioning equipment. Power conditioning equipment mitigates a power quality problem when it occurs.
These approaches are best captured with the flowchart from Electric
Power Research Institute (EPRI).
They provide an invaluable systematic methodology to solving power quality
issues.
In terms of cost of solution
Increasing Cost of Solution

Sensitive process machine
Usually the most cost effective solution is at the end-user level of the system.
In terms of troubleshooting

Basic steps of solving power quality problems
In terms of evaluation

Basic steps involved in a Power Quality problem evaluation
Caveat #1
Performing power quality investigations in and around energized equipment, exposed electrical buss work, and inside confined spaces can be dangerous. Testing and inspection of energized equipment should only be performed by qualified individuals familiar with proper safe work-practices.
Caveat #2
Follow all appropriate safety rules and procedures
– Company
– NFPA / NEC / IEE REGULATIONS (BS 7671) etc
–OSHA
– Appropriate state and local work rules
If All Fails…Call FullSpectrumenergy Energy, the Solutions Provider.
Contact us

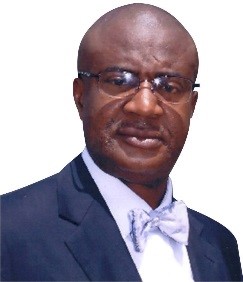
Victor Oyedu, FNSE, FNIEEE, CPQ.
Power Quality and Energy Management Specialist.
Publisher at Afrienergyonline.com
CEO, FullSpectrum Energy Solutions Limited, Nigeria.