
Industrial facilities are burdened with plethora of power issues in today’s manufacturing space.
From overheating of conductors, tripping contactors, circuits and relays, over/under voltages, equipment misoperation, electromagnetic compatibility, load unbalance, harmonic to power factor issues etc.
Resulting in expensive downtime, equipment malfunction, damage, high maintenance and energy costs.
Regrettably, engineers overlook the influence of Earthing & Lightning in troubleshooting, although power quality experts agree that earthing and lightning contribute to at least 80% of power problems in a facility. Therefore Earthing and lightning is the first line of action in eliminating and mitigating power challenges.
Simply by implementing improvements in earthing and lightning, industries can be safe, risks mitigated, operational efficiency improved, and bottom line enhanced.

There are 5 steps towards implementing effective Earthing and Lightning solutions to industry standards.
#1. Conducting Comprehensive Risk Assessment
Here you identify potential hazards related to earthing and lightning, such as electrical surges, equipment damage, and the risk of fire….By understanding the specific risks that exist within the facility.

Appropriate measures can then be deployed in design, construction and upgrades.
#2. Design Quality Earthing System.
An effective earthing system forms the foundation of a safe and reliable electrical infrastructure and provides a low-resistance path for electrical faults, preventing electric shocks and minimizing the risk of fire.

Upgrading the earthing system involves ensuring proper grounding of equipment, implementing surge protection devices, and considering the use of isolated grounding systems for sensitive equipment.
The above reduces electrical failures, equipment damage, and production downtime.
#3 Implementation of Effective lightning protection System (LPS.)

LPS to IEC/BS EN 62305, NFC 17-102 codes of practice eliminate direct and indirect (Surge) lightning effects on critical infrastructure. This proactive approach safeguards costly equipment failures, downtime, and potential injuries.
#4. Regular Inspection and maintenance.

LPS integrity tests to best practices should be carried out at least once annually. To ensure the continual integrity and effectiveness of the earthing and lightning systems.
It include and not limited to testing of grounding systems, inspection of lightning protection system, identification and rectification of any deficiencies.
Proactive maintenance is a sure way of arresting potential issues before they escalate, ensuring ongoing safety, reliability, and productivity of operations.
#5. Training and Education

Training and education on the importance of earthing and lightning solutions foster a culture of safety awareness among employees.
And empowers responsible staffs to identify potential risks, report any concerns, and follow proper protocols to minimize hazards. Training must include standards and guidelines for equipment grounding, surge protection, and lightning safety.
Improvement in earthing and lightning is not only a strategic investment but a significant one.

That assures safety of personnel & equipment, efficiency optimization, reducing downtime, and contributing to the long-term success of the manufacturing facility.
@Fullspectrum energy, our solutions help guarantee safety, seamless & efficient operations, profit in industrial manufacturing and other sectors without borders.

Call and book a free survey today!
Enquiries

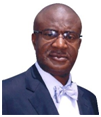
Victor Oyedu, FNSE, FNIEEE, CPQ.
Power Quality and Energy Management Specialist.
Publisher at Afrienergyonline.com
CEO, FullSpectrum Energy Solutions Limited, Nigeria.
@Fullspectrum