Background

The preponderance of electronics driving equipment in the residential, commercial and industrial work environment for efficient production of goods and service today.
These very sensitive electronics and microprocessors used in automation enhances efficiency. However, they come with inherent power quality concerns.
Premature failures, computer glitches, burned-out motors, loss of data are just some of the symptoms of power quality problems found in wiring systems of facilities that were designed for the needs of yesterday.
Yes, these symptoms met, and probably still meet, electrical standards and codes. But the codes are not intended to provide for a system free of transients, power surges, voltage sags, harmonics, spikes, and other interruptions that can cause expensive downtime or erratic data operations. An average facility experiences several of these power quality problems on a daily basis.

Most of these disturbances originate right within the facility.
Computers and electronics generate the very harmonics they’re sensitive to. Personal computers, laser printers and other switched – mode power supply equipment within your facility are usually the culprits for most of the power supply irregularities affecting other electronic equipment. It’s a problem that has only recently begun to be recognized in facilities as more electronic microprocessors and equipment are installed, turning the modern office or factory into a high – tech environment.
In new construction or renovation, many power disturbances can be prevented or significantly lessened by designing for power quality assurance, at surprisingly small cost.
In fact, the Electric Power Research Institute says: “inadequate grounding and wiring underline most problems with sensitive microprocessor-based equipment.”(EPRI Publication CU.2026.3.90).
The average additional cost to install enhanced electrical distribution system designed to the currently recommended practice versus a ‘standard’ system has been estimated to 2%-3% of the cost of construction. In upgrades or retrofits, the cost of solutions will run much higher, so the time to ‘do it right’ in initial design.
What does designing and constructing to power quality assurance hold in stock for facility stakeholders?
Landlord or Developer?
Savvy tenants know what to look for when shopping for space. They want a facility that meets their power needs now, and in the future. If your competitions is prepared for the modern facility, and you’re not, guess who gets the tenant?
Engineer or Contractor?
Your implementation of the power quality design considerations itemized here will impact electrical safety, reliability and allow design of a more functional facility resistance to the effects of harmonics and transients.
Factory or Industrial Facility?
The modern factory floor is a high-tech, interconnected manufacturing system. The cost of power quality problems in lost productivity, maintenance and repair at industrial facilities alone has been estimated at hundreds of billions of naira annually in Nigeria.
What is downtime or lost data worth in your facility, per hour?
The Solution

Fullspectrum energy solutions suggest the following steps to eliminate and/or mitigate most power quality problems from occurring:
- Use double-size neutral conductor or separate neutrals for each phase.
- Specify a separate, insulated full-size grounding conductor, rather than relying on the conduit alone.
- Use an isolated grounding conductor for sensitive equipment.
- Segregate sensitive loads on separate branch circuits, fed from a separate panel board, fed from a separate feeders (and even separate transformers if possible).
- Run a separate branch circuit for every 4 to 6 duplex outlets.
- Use an outside copper ground ring and multiple ground rods as part of the grounding electrode to achieve lowest practical resistance to ground. Measure ground resistance.
- Use harmonic rated circuit breakers, panel board, and transformers.
- Use surge and lightning protectors.
- Oversized phase conductors to minimize voltage drop. ( this will save energy too, and may even pay for itself through lower current squared resistance losses)
- Choose materials based on superior connect ability. Poor quality connections are a major consideration.
Designing these features into new construction or upgrades works. Reduces downtime, data loss and saves money, which will more than pay for these measures.

@ Fullspectrum solutions, we realize the significance of power quality in the workplace.
We are uniquely positioned to advise, design, implement power quality assurance to improve your facility overall business competitiveness and bottom line.
Remember, a quality job at first time saves money in the long run
Whenever, wherever and whatever the power quality needs.
Fullspectrum solutions is only a call or click away!
Enquiries
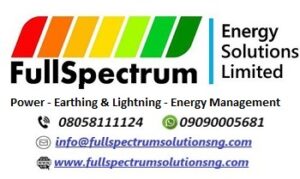
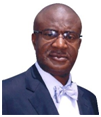
Victor Oyedu, FNSE, FNIEEE, CPQ.
Power Quality and Energy Management Specialist.
Publisher at Afrienergyonline.com
CEO, FullSpectrum Energy Solutions Limited, Nigeria.